Ad Details
-
Ad ID: 1358
-
Added: June 20, 2022
-
Views: 768
Description
What Do You Know About Laminated Bus Bars Guide
A bus bar, which is the part of the front end structure that is used to hang out electrical wiring or for structural support is known as the bus bar or the bus mast. This article is an attempt to explain what a bus bar is and what its different uses are. Busbars are usually aluminium (or sometimes steel) tubes that are commonly used to support an electrical cable in a bus setup. There are many different bus bars available that are made from different materials such as iron or aluminum. Some of the most popular bus bars are made from aluminium busbar current rated at up to 600amps, though busbars made from aluminium don’t necessarily have to be of this particular material.
The increasing tendency towards high power density systems in modern day manufacturing is another of the main reasons for the popularity of laminated busbars worldwide. The high power density leads to higher energy dissipation rates, and these lead to quieter operations, which are highly important when you consider the highly sensitive electronics that are often installed in bus garage setups. Furthermore, the high power density leads to better temperature control because the heat generated by the mechanical motion of the cables is dissipated away into the environment without being absorbed back into the mechanical components themselves. Current rating specifications for high power density busbars can go up to 600amps, which is a great deal higher than the current ratings for most other busbars on the market.
Another important factor for the performance of a laminated busbar is resistance to induction. Induction is a phenomenon where the magnetic field created by the conducting media tends to induce alternating currents within the conductive medium, which can in turn produce measurable levels of voltage. This effect is largely realized in high power configurations with inductance as the dominant form of resistance. Resistance to induction will depend greatly on the wire materials used to construct the bar, as well as the design of the induction coils used in the unit. The more even the resistance is from the induction field, the less potential power is generated by the device.
Another important consideration for the electrical performance of a laminated busbar is that of magnetic induction. This phenomenon has the effect of creating a field that exists parallel to the alignment of the conducting elements. It is believed that this phenomenon is what creates the dissimilar magnetic fields which produce the alternating currents we experience in our power devices. One popular theory suggests that the presence of a metallic layer permits the electrical current produced to be induced into a conductive metal core. This is the theory which is currently the only way to provide a good match between a laminated busbar and the required conductor, without giving either a voltage edge or an RF induction match.
There are several advantages to using a laminated busbar in electrical applications. For one thing, the smooth, flat surface of the unit allows for a smooth transition from one power element to another, without requiring abrupt movements. This also makes it easier to handle the power devices with a laminated busbar, since one does not need to worry about the resistance created by a metal layer. Also, if one requires a higher inductance, then there is an option to purchase a matching induction coil. With the appropriate sized coil, one can achieve a much higher voltage resistance than is possible when fitting a standard electrically conductive element.
The use of laminated busbars in electrical applications has the added advantage of extending the overall length of the cable, which can often be an issue in other applications. When a cable is too short, it is difficult to place the conductor in the best location, which may result in poor power quality or inconsistent current range. By using a laminated busbar, a power electronic device will be able to maintain a consistent current range, even when the current capacity is much larger than needed. In addition, this consistency in current distribution can also help reduce maintenance issues that can occur with poorly designed electrical components.
There are several different materials that can be used to produce laminated busbars, including copper, silver, gold, and stainless steel. Depending on the application and the electrical load, one of these materials will work best. For instance, a busbar made from stainless steel will have a much better thermal conductivity than a gold busbar, which will have a lower rating for thermal conductivity. Additionally, the gold version is often more resistant to rusting than other metals, such as copper. Since copper has a specified current range, it will be best used for high power electronics where extra current is needed. However, when current capability is much lower, it is acceptable to use a copper laminated busbar, which has a lower rating for thermal conductivity.
One way to check the resistance to moisture is to place a small amount of water inside a lubricated inductive gap insulated chamber. The water will conduct electricity and create an impression of an inductor. If this impression is clear, then the laminated busbar is capable of withstanding a higher level of moisture. When moisture passes through a conductor, it can increase resistance but also creates a large area of dead space. This means that the current cannot flow through the entire laminated busbar. With a proper moisture test chamber, however, this situation can be minimized and the electrical component will function properly.
What Do You Know About Laminated Bus Bars Guide
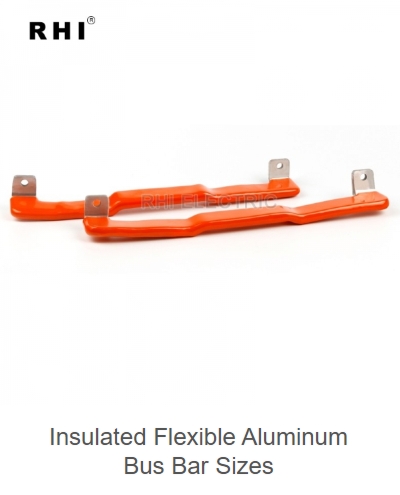